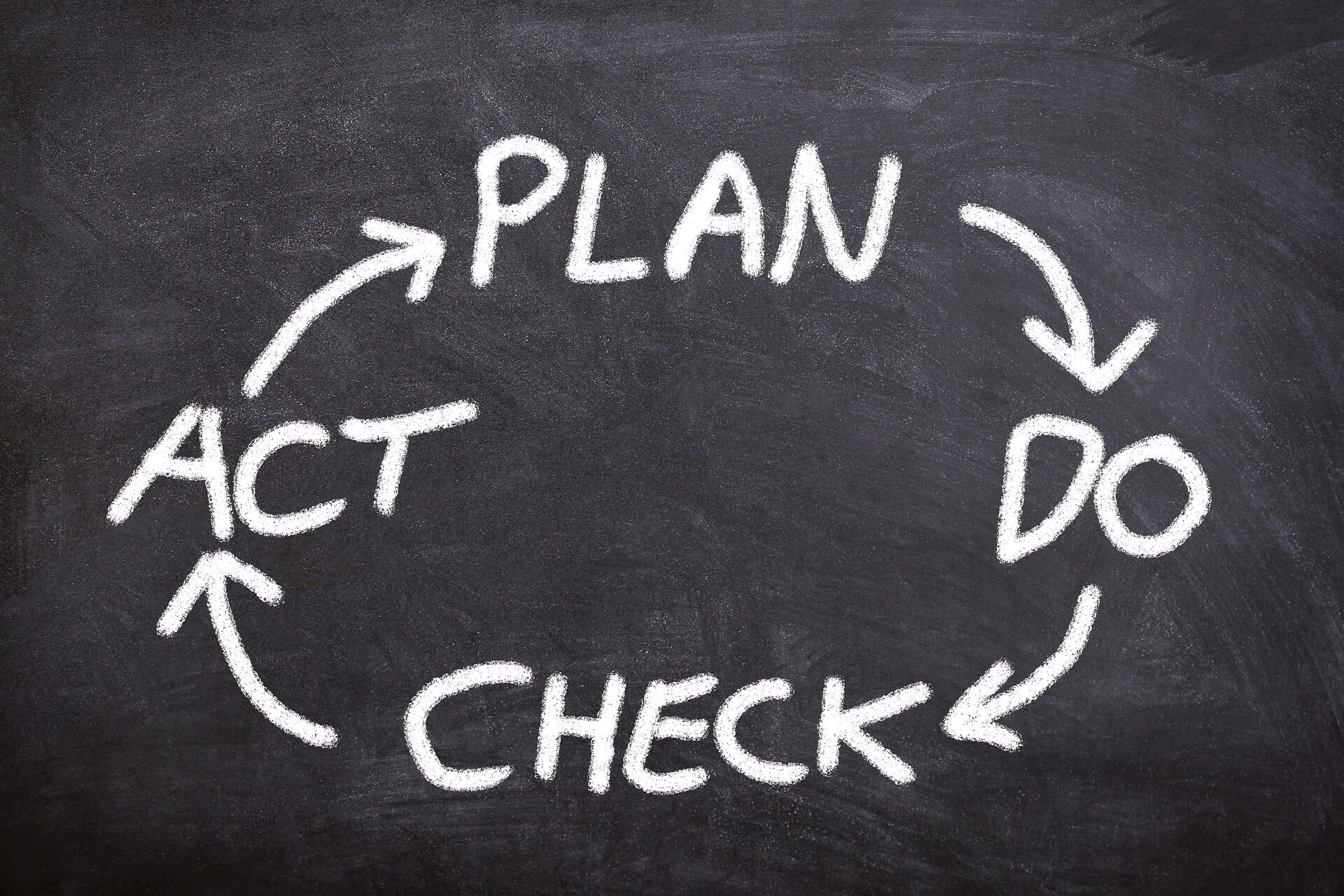
There is no denying that the price of any product plays a vital role in influencing customers to buy it. The other important factor is the quality. Any product which is of good quality will be able to continuously attract customers.
On the other hand, if the quality of the product is not up to the mark and is disappointing for the customers, then they will not buy the product, no matter how affordable the price.
This is a major reason why apart from price, businesses in the western part of China tend to focus on the capabilities of Chinese manufacturers to make products that meet customer expectations.
The process whereby quality is controlled during manufacturing provides businesses, regardless of their location, with a chance to ensure that the product meets all the specifications.
In China, all the skilled manufacturers conduct internal inspections during production, which serves as an integral part of the process. Buyers also recommend having a third party inspect the quality via an in-process check.
A third party could be the Chinese sourcing agent or companies which specialize in these types of inspections. This practice plays a key role in ensuring that products meet safety standards prescribed by government.
While the inspections are being conducted, the manufactured products are tested for all possible defects so that any potential issues can be solved on time. This further helps to manufacture the best possible product without any defects.
The primary reason for third party inspection in China is to identify the maximum number of potential problems before things to get out of hand, and the situation becomes unmanageable.
This is also done to ensure issues detected during manufacturing can be fixed without having to spend huge amounts of money. Manufacturers will have a clear understanding of what is acceptable and what isn’t.
With all this talk of precautions, it should be noted that errors do not often take place during production.
There are two major stages of inspections:
- Post-production or pre-shipping checks
- In-process checks
The inspections which take place during production are conducted by the relevant parties in order to make sure that any possible deviation is identified, while maintaining product specifications. This is also done to additionally check that all the pieces are consistent.
This is typically done when a good 20 % of the production process has been completed. If a company not only detects but also fixes issues during the production process, it then can prevent costly delivery delays.
Companies need to realize that it is better if the checks are not carried out too early in the production process. This is because the initial pieces off the assembly line are not perfect specimens.
Another reason is that as an integral part of their internal quality control checks, many factories tweak their respective practices once they have reviewed the first few pieces.
During pre-shipment inspections, inspectors appointed by the company run a quality check and also look for any type of problems which need to be fixed. These appointed quality inspectors make sure to look for areas of improvement which can be presented after the completion of the in-process inspection.
Inspectors often run a check on both the quality as well as the packaging of the product so that stakeholders can see if they meet the specifications of the customers.
What inspectors look for during in-process inspections
The people appointed by the company to perform quality inspection make sure that manufactured products meet the needs and requirements of customers.
The types of specifications can vary:
- Does the colour of the sample match the specifications?
- Are the dimensions within tolerance?
- Are materials used meet the nominated grades or standards?
If after inspection the company concludes that the product is not up to the mark, then they decide whether they can still accept this level of quality.
It is the job of the appointed inspectors to make sure that not just one, but every single product meets the necessary criteria. For example, if there are a couple of items which are defective, then this will point to a problem somewhere in the manufacturing process.
Furthermore, if some of the produced pieces are of great quality while some are defective, then the inspectors will conclude that the production process is facing a major issue and that immediate action is necessary. Such a situation indicates that the factory is failing to implement well-defined production controls.
In such critical situations it is considered best to get to the bottom of the problem by not only fixing the issue but by adding more production controls for the company.
After the problem is found during inspections
After the inspectors identify the problems, the next step is for the factories to rework the products and make sure that the problem is eliminated.
Sometimes, the reworking process turns out to not only be time-consuming but expensive as well. This can lead to further delivery delays.
If the application of the product is known to all the concerned parties, and also that the deviations will not cause harm in any way, there is a very high possibility of the faulty batch of products being labeled as safe. However, the next step is to fix the manufacturing process so that the remaining batches are free of issues.
A great example would be to imagine a water tap in a bathroom. One side of the water tap goes into the wall or the sink while the other side of the tap is exposed. If there is some sort of blemish on the sides of the tap which goes into the wall or the sink, then steps will be taken to clear the respective batch and alert the factory as well as the client.
Clients tend to accept the analysis at face value. There is also a very high possibility that the end-user might not even notice the defect.
With this being said, it is still an issue and needs proper fixing, so that further fixing can be done in the next prepared batches. All the fixing and detection depends on the usage as well as the situation. It is very important for companies to implement quality control during every stage of production.
It doesn’t matter whether the company is doing quality control for the first production cycle or for the hundredth time. Quality control ensures the consistency of products being produced.
Furthermore, it will also allow businesses to grow their customer base. Most of the factories in China produce products in large batches, and this is a major reason why the finished items do not often appear to be of good quality two weeks into the process of production.
The ideal time for inspection depends on the type of the product as well as the expertise of the factory. As soon as the quality inspector or the quality inspection team detects any sort of error in the production process, the factory is advised to implement corrective measures immediately.
If the company inspects the products after the process of production is completed, then this will be of no use and the company won’t be able to rectify the issue. Additionally, this will cause the company to face huge financial burdens.
The inspection conducted during manufacturing is the second most frequent type of quality inspection process. No matter the size of the business, this is type of inspection is adhered by all because of the impact on the final product.
The complexity of the process is not what is important; what’s important is for the inspection team to bring about the best possible solution.