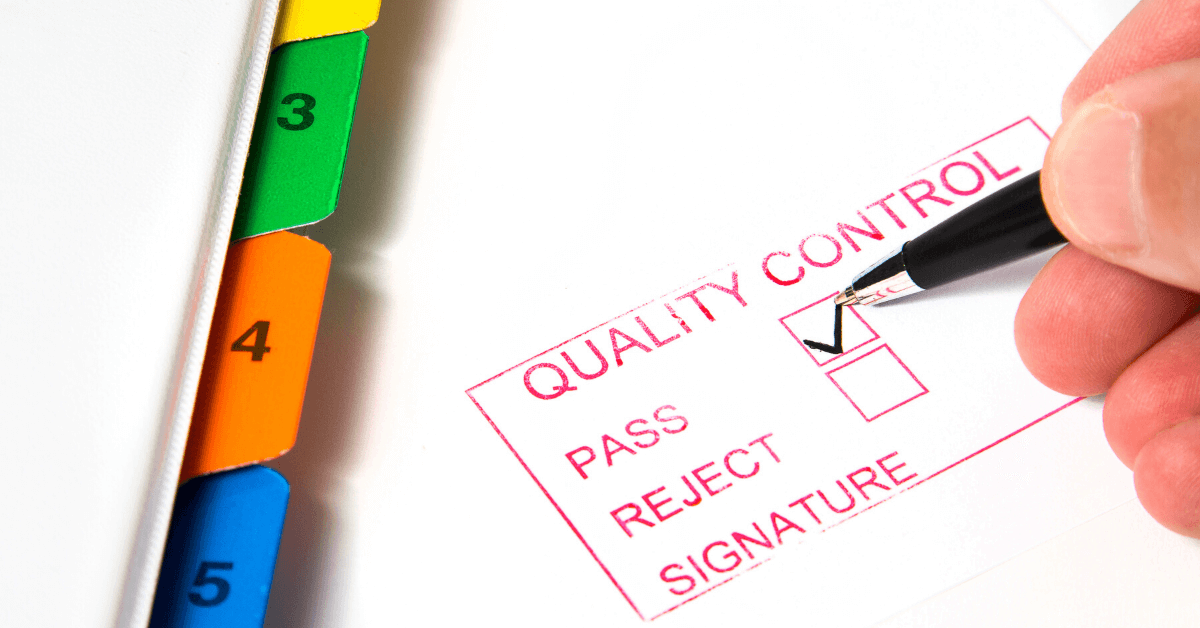
There are a lot of business owners running their business in the West who have made the important decision to shift their manufacturing to “low-cost” regions, such as China. However, this isn’t necessarily an easy operation.
Companies gradually relocate their production line to regions where manufacturing costs a fraction of what it does in the West.
There are many concerns facing business owners, among the most important is whether a certain factory in China will be able to manufacture products or components to the same set of specifications as the suppliers in regions like the US and Europe.
It points to the fact that the tag “made in China” is perceived to be a synonym for a low-quality product. There is absolutely no denying that up until a couple of years ago, products which were mass produced in China were of poor quality. Today, on the other hand, there are many factories in China which produce products that meet quality standards of the West.
The number of factors that have contributed to this change is huge. One of the most prominent reasons for this change is the level of exposure to the global market and the various requirements it holds. Another major driver for change is the growth rate of the middle class in China.
Middle-class consumers have proven to be a massive market for businesses. Furthermore, they are willing to pay more for higher quality products. Examples of such products include electronics, clothing, décor, sports and fitness, and toys.
A by-product of this is that China produces globally recognized brands: Lenovo, Xiaomi and Haier.
Experts in die casting, plastic injection moulding and metal stamping have been working in China for years. As a result, the quality of products has dramatically risen.
Acceptance of cultural differences and moving forwards
People not only in China but all over the world have different attitudes when it comes to quality. One great fact about China is that for many years the country has carried the title of the global exporter.
One common attitude common among the majority of the Chinese population is the “just about right” attitude. When a quality inspection is carried out by a stakeholder, the inspector may conclude that the product has a few unacceptable deviations. However, even after this declaration, the decision makers in the factory will say that the quality is “just about right”.
Obviously, this response does not to cut it and the process of inspection fails.
The producers may think, for example that a deviation in colour of 2 degrees or 2mm in dimension is acceptable.
However, a product with that level of deviation may be absolutely unacceptable for most buyers. As a result, manufacturers in China tend to think that people have become extremely picky in the international market.
With that being said, let us move on to the process of quality control and international standards.
What needs to be understood here is that the standards of quality audit in the West are not the same in China. Therefore, it is very important for the standard to be known to factories, as this derives the best results.
Chinese factories lacking quality control but have the awareness
If people auditing the working patterns and quality control of Chinese factories adopt Western standards, then they should expect two main outcomes.
The first scenario is that while the process of quality control ends up looking terribly on paper, the final products manages to meet the provided specifications.
The other probable outcome is that quality control certifies that the factory is producing products according to specifications, but the final product fails to meet the standards.
Why does this happen?
The process of quality inspection in the West includes having an in-process quality control officer. Appointing an in-process quality control officer in the factory may look professional since the factory has a person tasked with monitoring quality of products.
However, the real question facing the factory is whether the person who has been hired is suitable and qualified for the job.
The quality officer must not only look good on paper but must actually do his job well. For example, an old lady who uses calipers to inspect the production process and checks sample products for errors and issues is more effective than a young individual who has the necessary qualifications but doesn’t help to maintain quality during manufacturing.
Factories which are small in size tend to conduct the process of manufacturing only for niche segments, and all the employees working in those factories know all the ins and outs of the product and the production process.
Therefore, it is recommended to shortlist factories which have a good/impressive reputation in the market.
Furthermore, it is also advised to shortlist factories which have provided final products to Western countries. The major reason behind this is that it shows that the factory is familiar with standards in Western countries.
Another extremely important point is to discuss all the product specifications when negotiating a partnership. It is important that all the requirements have been communicated to the factory as clearly as possible to avoid confusion.
You should either hire quality control inspectors or carry out the process of quality control in-house. There are many factories that are very much open to quality inspections.
Therefore, avoid collaborating with a factory which resists quality inspections.
The cost of manufacturing is directly proportional to quality
The manufacturers will have a price floor, which refers to minimum costs which are necessary to safeguard the quality of the product. This refers to cost of water, electricity, operating of the machinery, etc.
Large buyers often times try to lower the price set by the supplier, and they frequently succeed because they have more power and leverage. A supplier could be willing to negotiate down their price if the size of the order is large.
However, what everyone needs to understand is that a drastic and unnatural reduction in price will have its own repercussions in the future. This usually results in the use of low quality raw material, hiring ill-equipped and low-skilled workers, and employees not being provided with appropriate working conditions. All of these factors will have an adverse effect on the quality of the final product.